Mesurer les diamètres intérieurs
Vérifier avec précision les tolérances dimensionnelles des alésages permet notamment d’assurer leur bon ajustement (jeu et serrage) lorsqu’ils sont assemblés avec un arbre mécanique.
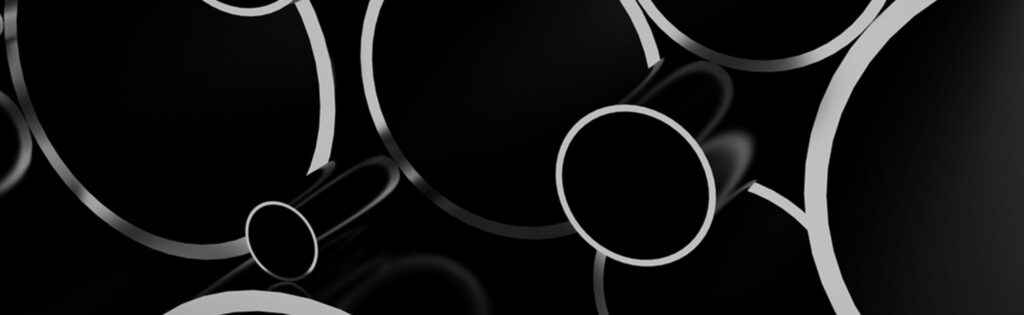
Pourquoi contrôler des diamètres intérieurs ?
L’enjeu principal des contrôles de diamètres intérieurs est de vérifier que l’alésage d’une pièce usinée lui permettra d’assurer sa fonction principale : s’ajuster correctement avec un arbre.
Selon l’application, cet assemblage peut présenter un jeu (l’arbre, de diamètre inférieur à l’alésage, peut glisser dans celui-ci, comme dans le cas d’un piston moteur dans son chemisage) ou un certain niveau de serrage (l’arbre, de diamètre supérieur à l’alésage, est alors solidaire de celui-ci après montage, comme dans le cas d’un engrenage sur un arbre moteur).
Des outils très simples tels que des pieds à coulisse, alésomètres ou micromètres d’intérieur peuvent être utilisés, mais ne disposent pas de la précision, du niveau de traçabilité ou d’automatisation demandé par de nombreuses industries
Le contrôle de diamètres d’alésages par la méthode pneumatique
La mesure pneumatique est largement utilisée dans les processus de fabrication et de contrôle de la qualité pour vérifier les diamètres intérieurs des pièces fabriquées.
La méthode emploie la technologie des tampons ou jauges de mesure pneumatiques. Ces jauges utilisent de l’air comprimé pour mesurer le diamètre intérieur d’un trou ou d’un alésage. La jauge se compose d’un cylindre creux avec au moins deux petits orifices à son extrémité. Elle est insérée dans le trou ou l’alésage à mesurer.
De l’air comprimé est introduit en permanence dans le cylindre, et sort par les orifices. La pression de ce flux d’air varie en fonction de l’espacement entre les orifices et les bords de l’alésage contrôlé. La pression qui en résulte est mesurée pour déterminer les dimensions internes du trou ou de l’alésage.
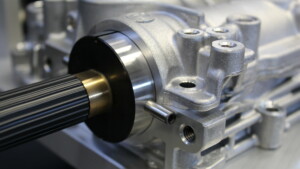
C’est plus précisément la différence entre cette pression et la pression de l’air comprimé en amont qui est mesurée, par un dispositif appelé débitmètre pneumatique, colonne de mesure ou comparateur pneumatique. Il matérialise cette différence de pression par une hauteur de liquide ou par sa représentation graphique sur un logiciel. Cette hauteur de liquide est comparée à celle obtenue pour des pièces étalons de diamètres souhaités.
Les jauges pneumatiques offrent plusieurs avantages par rapport à d’autres types d’outils de mesure pour contrôler les diamètres intérieurs, notamment une grande précision, une mesure sans contact et la possibilité de mesurer des formes et des géométries complexes. Elles sont couramment utilisées dans des industries telles que l’automobile, l’aéronautique, la défense et les dispositifs médicaux pour garantir la précision et l’exactitude de la production des composants : chemisages de pistons, roulements, fûts de canon, corps de seringues, etc.
Le contrôle de diamètres intérieurs par les méthodes tactiles
La technologie tactile peut être employée pour mesurer des diamètres internes de pièces, et en particulier les palpeurs numériques, à déplacement linéaire (LVDT), à déclenchement par contact, ou les palpeurs de scanning. Ces capteurs sont portés par une machine et mis à proximité de la pièce à contrôler. La machine contrôle donc leurs positions dans l’espace. Ils sont mis en mouvement jusqu’à détection d’un contact avec la surface de la pièce à vérifier. Les coordonnées des points de contact sont alors enregistrées.
Ces coordonnées sont comparées pour calculer le diamètre intérieur contrôlé. Selon la technologie employée, les palpeurs mesurent soit deux points fixes, soit une série de points le long de l’alésage.
Du fait de l’encombrement de ces palpeurs, ces technologies sont toutefois réservées à des alésages relativement larges. Par ailleurs, le principe même de la mesure tactile les réserve à des pièces dont la surface ne risque pas d’être endommagée par un contact avec le palpeur.
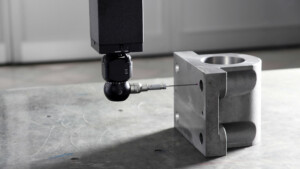
Contrôle manuel, automatique, analogique ou numérique ?
Si la méthode pneumatique est traditionnellement manuelle, elle peut, tout comme les méthodes tactiles, utiliser des automatismes et robots pour la prise des pièces, le déplacement des palpeurs ou des tampons, voire le tri des pièces en fonction de leur conformité ou non. Ces automatismes sont totalement adaptables aux types de pièces et besoins de cadences de mesures de l’utilisateur. Ils sont généralement conçus, assemblés et programmés par le fournisseur.
Par ailleurs, divers logiciels peuvent être employés pour enregistrer les résultats de mesures ou de comparaisons de diamètres.
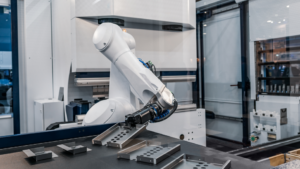
Dans le cas de la mesure tactile, les logiciels peuvent reconstituer une imagine numérique à partir des coordonnées mesurées. Les diamètres souhaités peuvent alors être déterminés sur cette image numérique par un algorithme ou par l’utilisateur via une fonction de traitement de l’image du logiciel.
De plus, l’enregistrement des données de mesure et la gestion des comptes administrateurs ou utilisateurs offrent un niveau de traçabilité que les systèmes analogiques ne peuvent égaler.
Dans le cas de la mesure par palpeur, le logiciel peut générer une image numérique à partir des coordonnées mesurées. Comme dans le cas des mesures optiques, l’image peut ensuite être analysée à l’aide d’un algorithme ou d’une fonction de traitement d’image pour déterminer les diamètres souhaités.
TECHNOLOGIES SETSMART ASSOCIÉES
Parcourez les pages technologies pour plus d’informations sur les moyens de contrôle mis en œuvre
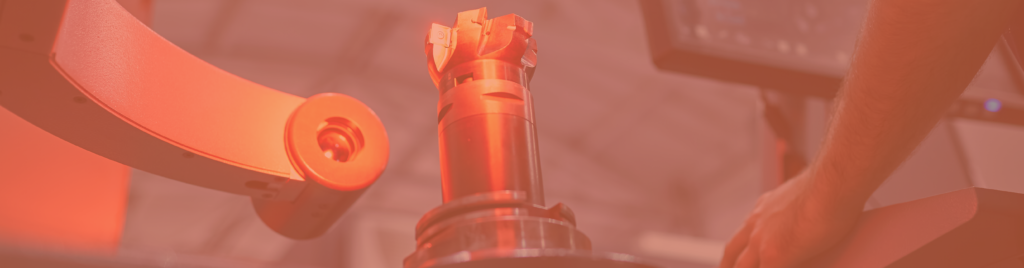