Présentation de la technologie des colonnes de mesure pneumatiques
Les colonnes de mesure pneumatiques sont des outils de mesure couramment utilisés au cours des procédés de fabrication, pour le contrôle de la qualité des pièces produites. Ces outils utilisent les variations de pression d’un flux d’air comprimé pour déterminer rapidement les dimensions et les paramètres géométriques des pièces testées avec exactitude et précision.
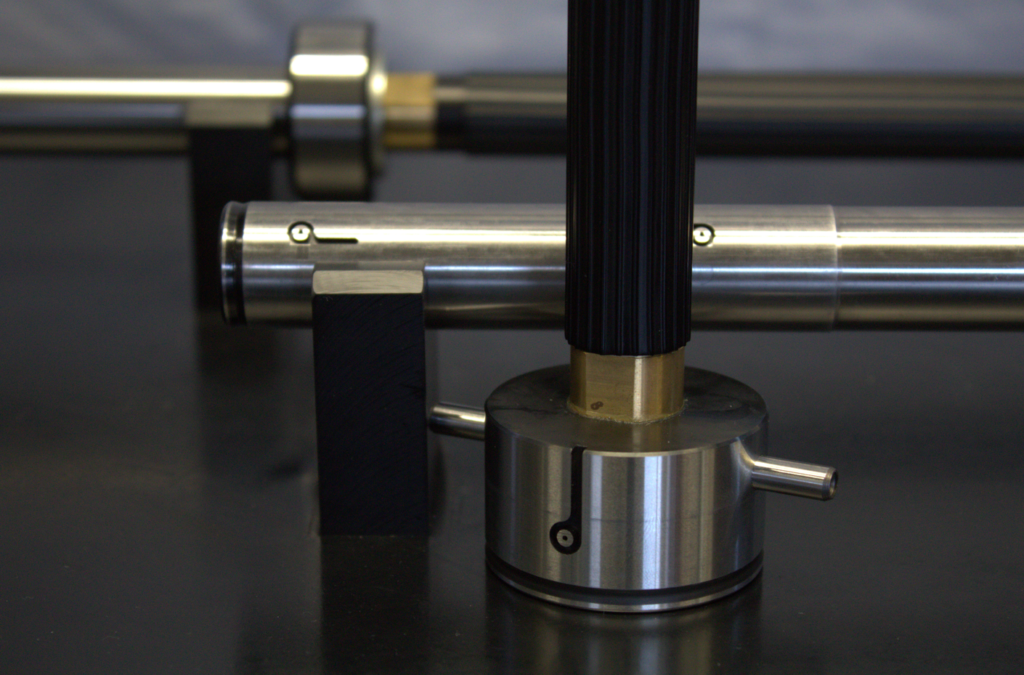
Introduction à la mesure pneumatique
Principe de la colonne de mesure
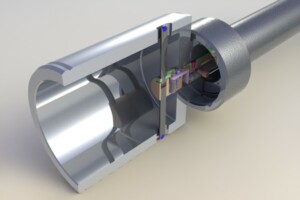
Avantages des colonnes de mesure pneumatiques
Les colonnes et tampons pneumatiques offrent plusieurs avantages par rapport à d’autres outils de mesure. Ils sont très exacts et répétables, ce qui les rend idéaux pour les processus de fabrication et de contrôle de la qualité, où même de petites variations de dimensions peuvent avoir un impact significatif sur les performances et la résistance à l’usure du produit. Ils utilisent une méthode de mesure sans contact, éliminant ainsi le risque d’endommager des pièces d’essai délicates ou sensibles aux frottements.
-
Simple et rapide
Mesures réalisées en quelques secondes, indépendantes des compétences de l’utilisateur
-
Sans contact
L’état de surface de la pièce contrôlée est préservé
-
Exacte et répétable
Excellentes performances métrologiques
-
Directement dans l’atelier
Quel que soit sa propreté