Contrôler les orifices micrométriques
De nombreuses pièces manufacturées disposent d’orifices qui assurent leur fonction principale. Contrôler le diamètre, la forme et l’absence d’obstruction de ces orifices permet d’assurer que la pièce réalisera correctement sa fonction principale.
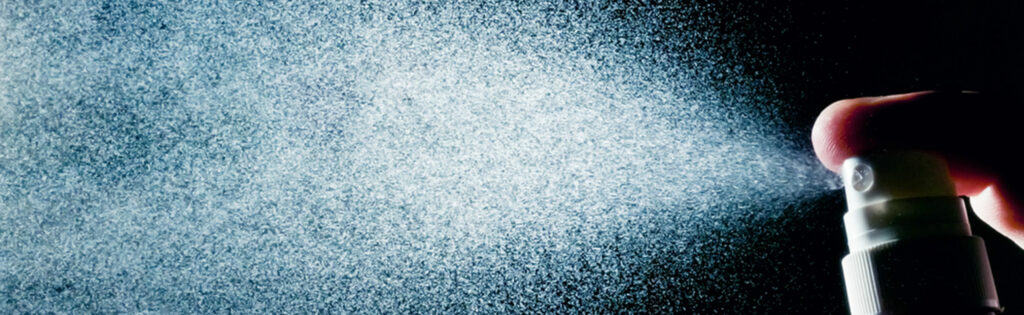
Les enjeux du contrôle d’orifices
Les dimensions internes de petits orifices sont plus difficiles à mesurer, donc à contrôler que des alésages ou ouvertures plus grands. S’il existe des outils de mesure dimensionnelle tels que des pieds à coulisse ou des jauges d’alésage, ces techniques ne sont simplement plus applicables pour des orifices de l’ordre d’un millimètre de diamètre ou moins.
Et pourtant, ces orifices, leurs diamètres et leurs formes peuvent avoir une fonction critique pour la pièce qui les porte. C’est par exemple le cas de buses de pulvérisation industrielles, de boutons actionneurs de sprays aérosols pour la cosmétique ou la pharmacie , d’ouvertures d’aérations pour des pièces soumises à des températures élevées, etc.
Ainsi l’entreprise en charge de la fabrication en série de ce genre de pièces, si elle est capable d’assurer leurs paramètres géométriques, confortera en même temps son client sur la qualité des produits qu’elle lui fournit.
Le contrôle d’orifices par la méthode pneumatique
La mesure pneumatique est une méthode basée sur l’analyse de la variation de pression consécutive aux variations du débit d’un flux d’air au travers d’un orifice.
Le dispositif qui permet cette mesure est appelé un débitmètre pneumatique, une colonne de mesure, ou un comparateur pneumatique. Il est principalement constitué :
- D’un système de régulation de la pression du flux d’air circulant dans le dispositif.
- D’une sortie de ce flux d’air vers l’extérieur : le flux d’air est dirigé vers l’orifice à contrôler à l’aide d’une pièce d’adaptation. La pression de sortie du flux d’air dépend de la dimension et de la forme de l’orifice.
- D’un système de détection de la différence entre la pression interne et la pression de sortie. Le système de détection est typiquement une colonne de liquide dont la hauteur dépend de la différence de pression, ou sa représentation graphique sur un logiciel.
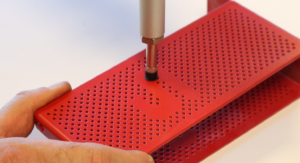
La méthode consiste tout d’abord à mesurer cette différence de pression sur un ou des orifices étalons jugés bons ou mauvais : valeur cible, tolérance minimale, tolérance maximale. Les hauteurs de liquide correspondantes sont repérées.
Puis la série de pièces à contrôler est mesurée, et les valeurs de différences de pressions sont comparées aux valeur cibles et limites déterminées.
Outre des non-conformités sur les diamètres et les formes des orifices, la méthode permet également de détecter des phénomènes d’obstructions, puisque ces obstructions provoquent une augmentation de pression due à l’impossibilité du flux d’air à circuler dans l’orifice.
Contrôle analogique ou numérique ?
Comme indiqué plus haut, certains dispositifs traduisent la dimension de l’orifice en une valeur numérique indiquée sur un graphique.
Les logiciels qui permettent cette représentation disposent également de fonctions très intéressantes pour l’utilisateur : la programmation de procédures (ou gammes) de contrôle de divers types d’orifices, l’affichage de résultats de mesure simples pour une prise de décision rapide, des calculs statistiques sur des séries de résultats, la génération automatique de rapports de mesures.
Grâce à l’enregistrement des données de mesure et à une gestion de comptes administrateurs ou utilisateurs, ils offrent également un niveau de traçabilité des résultats de contrôle des orifices micrométriques qui n’est pas possible avec des systèmes analogiques.
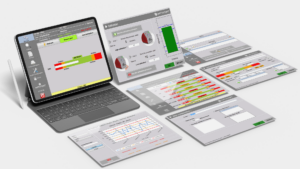
TECHNOLOGIES SETSMART ASSOCIÉES
Parcourez les pages technologies pour plus d’informations sur les moyens de contrôle mis en œuvre
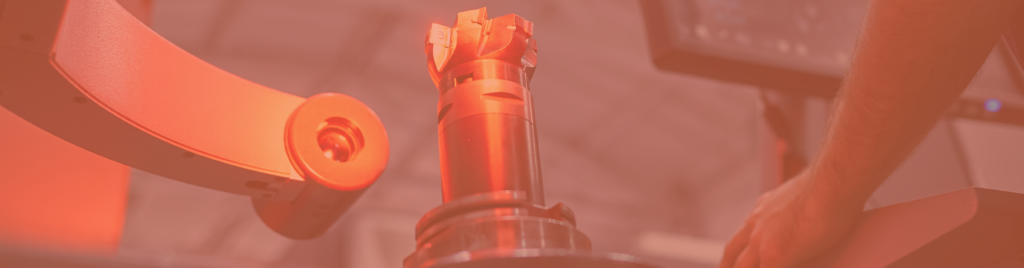