Outer diameter measurement
Complying with outer diameter specifications for parts such as tubes, shafts or axles is a challenge for their manufacturers. Pneumatic, tactile or optical methods can address these needs.
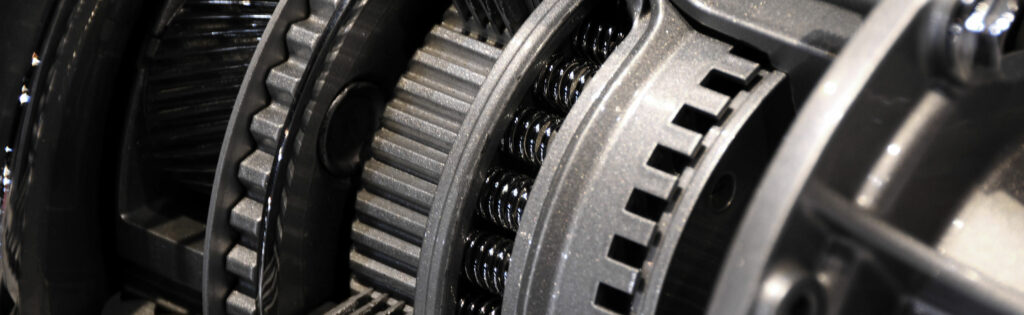
Why controlling outside diameters?
Controlling the diameters of tubes, shafts or axles by the pneumatic method
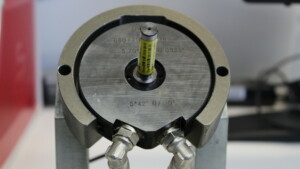
The pressure of the air flow varies according to the spacing between the orifices and the edges of the controlled part. The measured diameter is materialized by a height of liquid which depends on this pressure, or by its graphical display on a software. This height of liquid is compared to the one obtained for standard parts of the desired diameters.
Ouside diameters control using touch probes
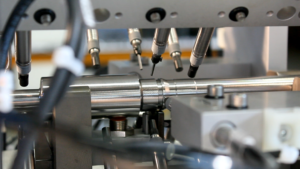
The technique is quite universal and allows, depending on the sensors and robots chosen, to design machines specialized in the control of certain families of parts or very versatile machines capable of controlling a large number of different parts. The touch probe technology principle does not allow the inspection of parts whose surface could be damaged by contact with the probe.
Ouside diameters control using industrial vision
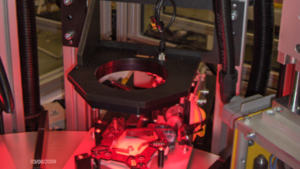
In addition to their accuracy and non-contact measurement method, optical micrometers are also easy to use and can measure a wide range of object sizes and shapes. The high measurement rate of optical micrometers and the fast processing speed of the software allow this method to be used in-line, directly on the manufacturing process.
Manual, automated, analog or digital control?
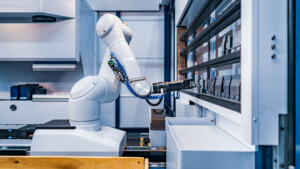
ASSOCIATED SETSMART TECHNOLOGIES
Visit the technology pages for more information on the control techniques used
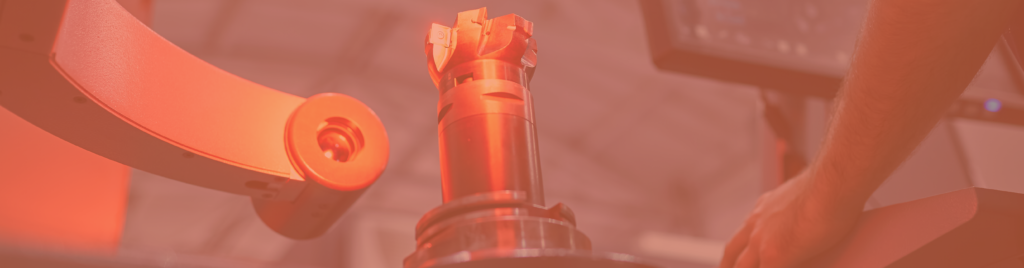