Industrial machine vision and optical metrology in a nutshell
Solutions based on industrial machine vision and optical metrology, because they combine automation, digitalization and flexibility, play a decisive role in smart factories and industry 4.0.
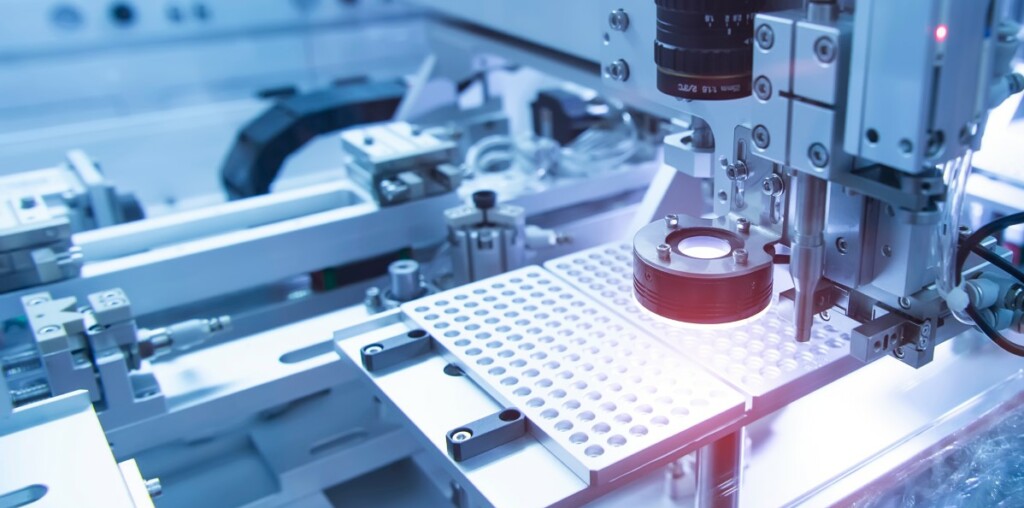
Introduction to machine vision and optical metrology
Optical metrology and machine vision represent key technological fields in the production and quality control sectors. What they have in common is the use of sophisticated light sources and camera systems to provide precise dimensional measurements, and to inspect and control various aspects of manufactured objects, ranging from external dimensions to subtle characteristics such as the presence of defects or compliance with specific standards.
These technologies play a key role in the automation of manufacturing processes, offering fast, precise and non-invasive solutions for guaranteeing product quality and optimizing industrial operations. Thanks to robots and automation, the speed of these systems is remarkable, enabling efficient on-line or at-line operations.
Optical and vision inspection principles
In optical metrology or machine vision technology, the measuring core comprises digital cameras, lenses, and a lighting system.
Optical micrometers, utilizing light sources such as lasers or LEDs coupled with receptors like CCD or CMOS sensors, serve as versatile systems for dimensional measurements. Positioned between the light source and receptor, the inspected object interrupts the light beam, and the shadowing generated is analyzed by an image analysis algorithm. It can determine the dimensions and important geometric specifications that the object must meet in order to be declared compliant.
In machine vision, one or more cameras capture images of the objects to be inspected. They are selected according to the suitability of their properties (color or monochrome, angle of view and depth of field, resolution, sensitivity, file transfer time) for the pictures to be taken. The lighting system is strategically chosen to highlight essential parts of the object, adjusting brightness, contrast, etc. Image processing software further refines images and applies algorithms for measuring dimensions, checking colors, ensuring correct assembly of sub-parts, detecting foreign particles, stains, scratches, chips, and more.
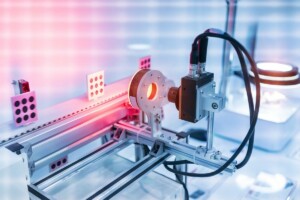
Benefits of optical metrology and industrial machine vision
Both optical micrometers and industrial vision technology offer a range of benefits.
Optical micrometers are versatile, accommodating various object types, dimensions, and geometries, providing measurements against tolerances. The technology is contactless, fast, and supports online operations.
Industrial vision, on the other hand, is extremely versatile, inspecting diverse objects and parameters, with a focus on dimensions, assembly, shapes, or aspects. Once set and programmed, inspections become fast, reliable, and sustainable, offering user-independent and autonomous capabilities.
The automation of measurement systems based on these two technologies means that traditional visual inspection operations can be carried out at a faster pace. The precision and repeatability of part handling and positioning controlled by automation systems and other robots also enhances inspection reliability. Finally, both technologies are advantageous for soft, flexible, brittle, or mechanically fragile materials due to their contactless nature.
-
Versatile
Numerous simultaneous measurements on the same part
-
Contactless
Non-intrusive technology, applicable even to soft or fragile materials
-
Accurate and repeatable
Excellent metrological performance
-
Simple and fast
Measurements performed in seconds, independent of the user’s skills
Related products
-
Inspex OUT
For high throughput and precise inspection of the assembly, aspect, or surface finish of your products.