Why has metrology software become so essential in industry?
Software employed in metrology and machine vision plays a key role in the context of Industry 4.0, marking a significant evolution in the way companies approach production and quality. Their adoption contributes to more efficient, flexible and intelligent production, boosting companies’ competitiveness in the global marketplace.
The combined use of machine vision and metrology, supported by specialized software, helps to ensure the quality, precision and efficiency of manufacturing processes in various industrial sectors, such as automotive, aerospace, electronics and consumer goods production.
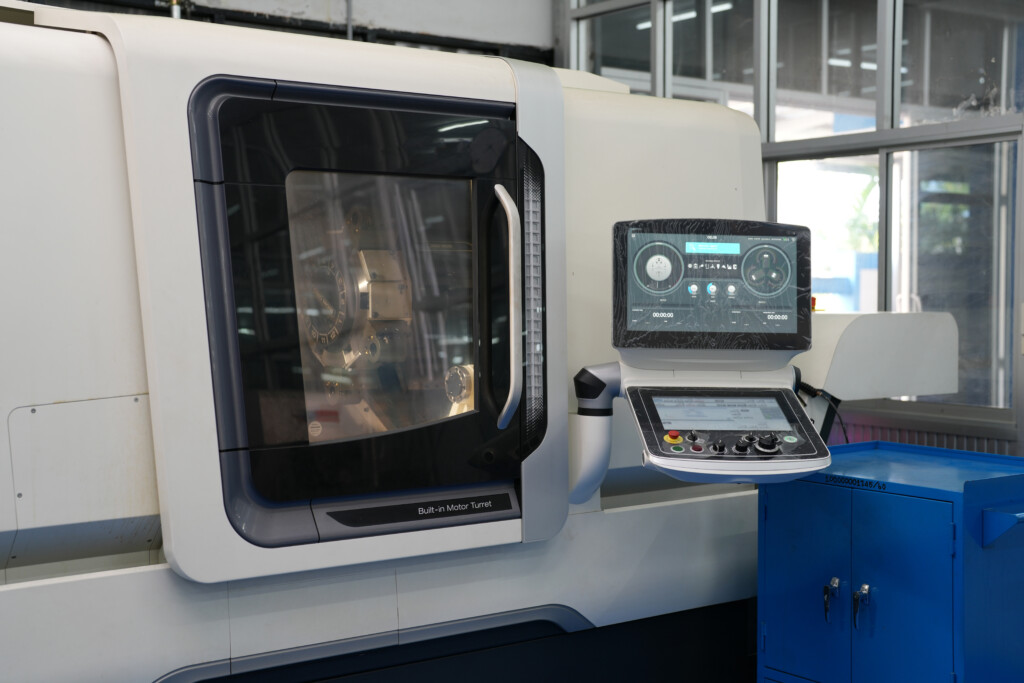
What is metrology and machine vision software?
This type of software controls a machine dedicated to industrial measurement or inspection, generally used to check the dimensions, correct assembly or lack of defects of a part or product being manufactured. In addition to this control function, the software acquires, analyzes, records and transfers inspection data.
In particular, machine vision software can analyze images or videos captured by industrial cameras. They can extract specific dimensional information, locate objects or sub-assemblies, and identify defects by comparing the captured pictures with references of compliant and non-compliant parts.
This software enables product traceability to be tracked and documented throughout the manufacturing process. This can include information on suppliers, production dates, manufacturing stages, etc.
Often designed to integrate with other systems within the plant, such as production management systems (ERP), quality control systems, or even the production machine itself, this software contributes to the smooth coordination of industrial processes.
Key features of metrology and machine vision software
Metrology and machine vision software can offer a wide range of functions, depending on the purpose for which they are used.
- User communication
Software can be hosted on one or more human-machine interfaces (HMIs), such as PCs, laptops or digital tablets, in their classic or ruggedized versions for workshop use.
They are adapted to the type of user (operators, metrology experts or maintenance engineers) in terms of ease of use and support.
They feature functions for displaying measurement data and generating control or inspection reports, including production logs, control charts, statistical data processing, or process capability calculations.
- Communication with measurement tools
Software also interfaces with the inspection machines it is designed to control. They exchange parameters for setting procedures, calibration, sensor management and, of course, measured parameters, tolerances, etc.
- Defect detection
In the case of machine vision software, image processing functions are very important. In particular, they are used to recognize, control and detect object defects using reference data libraries (good and bad parts).
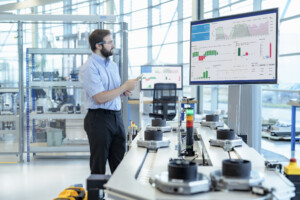
- Automated quality control
These software packages offer automated qualification of results (good / doubtful / bad). They measure, detect and display non-conforming parts in real time. They can inform operators or a supervisory system of these non-conformities.
- Traceability management
Software is also used to ensure traceability of controls or inspections. In this way, measurement results are attached to the identification number of the parts tested, and modifications to test results are traced, etc. Software often also offers a system for managing user profiles and rights.
- Integration with other systems
This family of functions enables the software, via analog or digital inputs and outputs, to interact with automation systems, safety systems, robots, other measuring instruments, and even production machines. Orders and information are exchanged, as diverse as calibration requests, measurement start commands, measurement status information, warnings based on tolerance thresholds, and action commands can be sent or received. Via a computer network (FTP server), a Supervisory Control and Data Acquisition (SCADA) system or a Distributed Control System (DCS), the software can interact with manufacturing tools for dynamic corrective actions, such as adjusting manufacturing machine parameters.
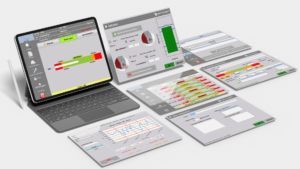
The benefits of metrology software for the industry
In the digital landscape mapped out by the Industry 4.0 movement, metrology software offers a range of key benefits. First, they enable real-time data collection, providing immediate visibility of production process performance. This ability to monitor continuously helps to quickly identify quality deviations and take instant corrective action, thus reducing errors and waste.
Moreover, metrology software facilitates the integration of measurement data with other systems within the plant, creating a connected ecosystem. This interconnectivity promotes more informed decision-making, as metrological information is seamlessly shared with other departments such as production, planning and maintenance.
Automation is another key aspect. Metrology software enables measurement processes to be automated, reducing dependence on human intervention and minimizing the risk of error. This frees up skilled personnel for higher value-added tasks, while guaranteeing greater measurement accuracy and repeatability.
Finally, these technologies make it possible to anticipate potential failures, optimize measurement processes and adapt parameters in real time to maintain optimum quality levels.
In this way, metrology software is becoming not only a quality control tool, but also a key player in the digital transformation of industry. Their adoption as part of Industry 4.0 contributes to more efficient, flexible and intelligent production, boosting companies’ competitiveness in the global marketplace.