An overview of pneumatic comparators and air plug gauges technologies
Pneumatic comparators and air plug gauges are two types of measurement tools commonly used in manufacturing and quality control processes. These tools operate on the principle of using air pressure to quickly determine dimensions and geometrical parameters with accuracy and precision.
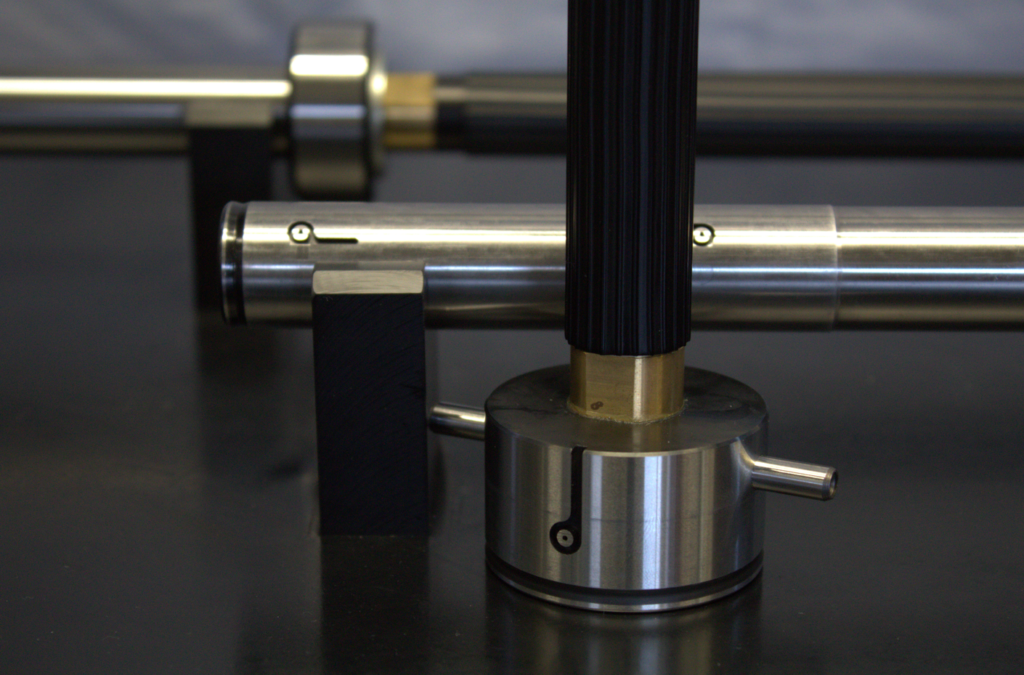
Introduction to measurements by pneumatic comparators
Many types of manufactured parts must respect strict dimensional and geometrical specifications. This may be to perform their primary function correctly or to ensure that they are mechanically assembled to the desired fit.
Current methods such as Coordinate Measuring Machines (CMMs) are very accurate, but their operation is relatively slow and often requires a clean, temperature-controlled environment, conditions that are not readily met on the shop floor. In addition, they are often expensive and their use requires qualified personnel.
Pneumatic measurement, although less universal than CMMs, combines measurement simplicity, speed and use by non-specialists in most shop floor environments in the industry. It is capable of measuring with micrometer accuracy.
Principle of pneumatic comparators and air plug gauges
The pneumatic comparator, which is the basic module of the measuring system, is connected to a source of compressed air creating a reference pressure. The part to be tested is then connected to the same source of compressed air: either directly when testing a small orifice (e.g. the orifice of an aerosol spray nozzle), or via a measuring air plug or air ring (e.g. to measure the diameter of a bore or a drive shaft). The resulting pressure is measured. The difference between the reference pressure and the test piece pressure is represented by a liquid height in the case of analog comparators or by a graphical representation in the case of digital comparators.
The method uses reference standards or templates, measured under the same conditions. By comparing the liquid heights or their numerical equivalents obtained, we can then determine the conformity of the tested part to its dimensional or geometrical specifications.
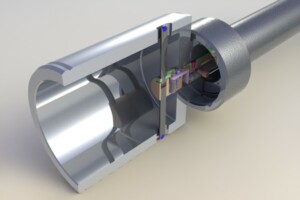
Benefits of the pneumatic comparators technology
Pneumatic comparators and air gauges offer several benefits over other measuring tools. They are highly accurate and precise, making them ideal for manufacturing and quality control processes, where even small variations in dimensions can have a significant impact on product performance and durability. They use a non-contact measurement method, eliminating the risk of damaging delicate or friction-sensitive test parts.
-
Simple and fast
Measurements performed in seconds, independent of the user’s skills
-
Contactless
The surface condition of the tested part is preserved
-
Accurate and repeatable
Excellent metrological performance
-
Directly in the shopfloor
No matter how clean it is